政井「まずはNTTデータの政井から、昨今の製造現場が抱える課題についてご紹介します。製造業を取り巻く環境は近年めまぐるしく変化しています。それに伴って製造現場でも外部環境ならびに会社内が変化していくなか、QCD のさらなる改善に加えて環境負荷の低減も要求されています。職場の安全、人材の育成、働きやすい職場を実現しつつ、これまで以上に工程の改善や設備効率の向上を目指すことが求められています。
そんななか、OTを中心に活用する製造部門、ITを中心に活用する管理部門の特徴の違いから壁ができてしまう、という課題にお悩みではないでしょうか。
例えば製造部門であれば、現場を止めない、品質を確保する、安全を担保する、といったところが命題になってきます。一方で管理部門では、機密情報や個人情報を守る、低コストで運用するなどが命題となってきます。トラブル時も、製造部門は生産再開をまず中心に考えますし、管理部門はデータの保護や再発防止の徹底を考えるのではないかと思います。このようにOTとITは専門用語の違い、価値観の違い、組織の違いといった壁があり、そのせいでリアルタイムでのデータ連携やデータ資産を作っていくうえでの課題があると考えております」。
Event / Seminar イベント・セミナー
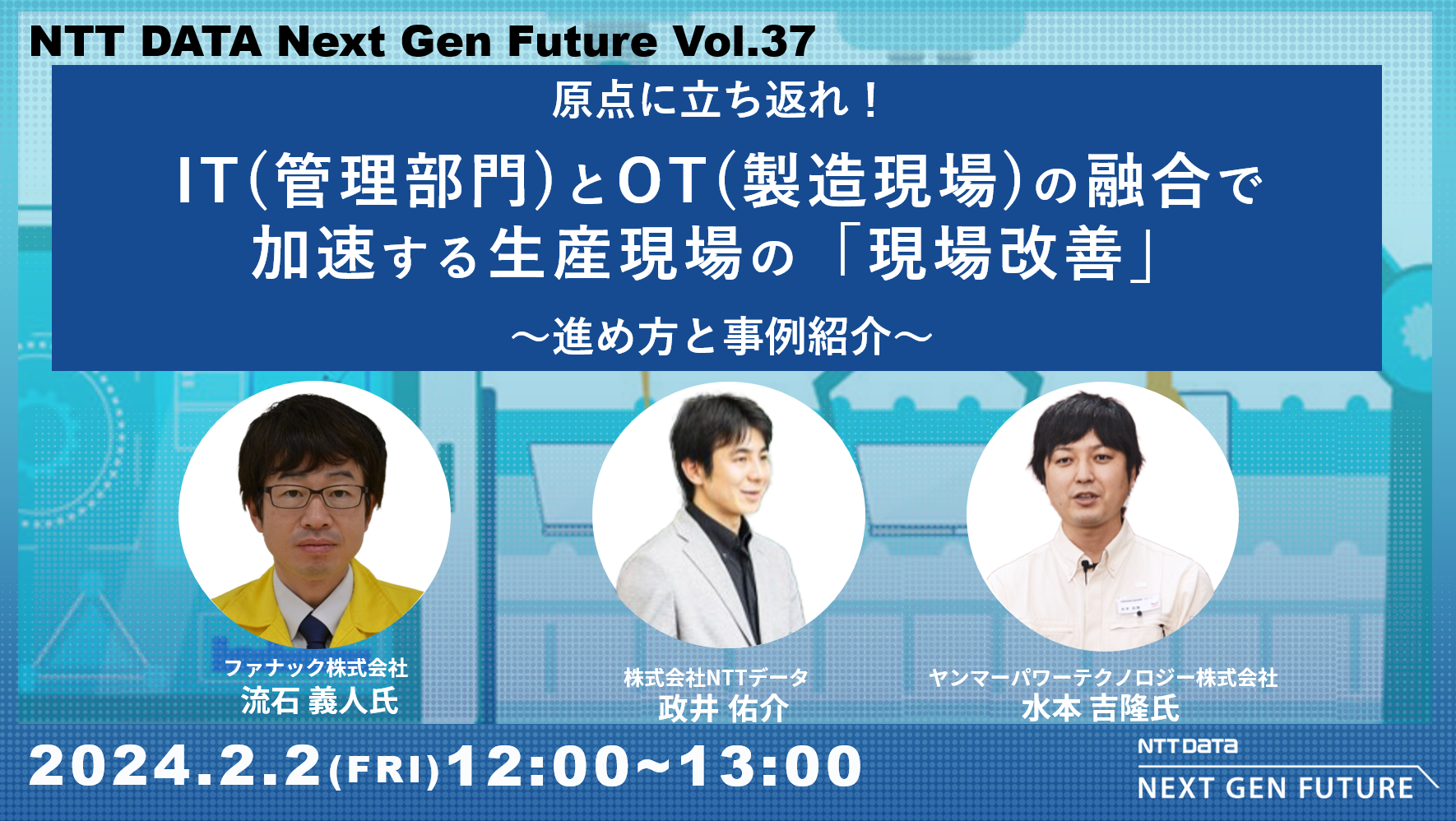
NTT DATA Next Gen Future vol.37
IT(管理部門)とOT(製造現場)の融合で加速する生産現場の「現場改善」
工場のスマート化・DX化が叫ばれて久しいが、個別改善やツールのPoCで止まってしまい、成果の刈取が出来ずに活動が止まってしまっているケースが散見されます。 また、改善・改革に必要なデータを取得・活用する為には、現場設備の中心となるOTデータと管理部門のITデータ双方のノウハウ及び専門的な業務知識を保有している必要があります。 これら製造現場のDXで陥りがちな課題とそれを解決する「改善活動の進め方」と「NTTデータ×FANUCによる改善サポート」をご紹介します。
このような方におすすめ
- ・製造現場で改善活動を推進している方、課題を抱えている方、悩んでいる方
- ・DX部門で製造領域のプロジェクトを推進されている方
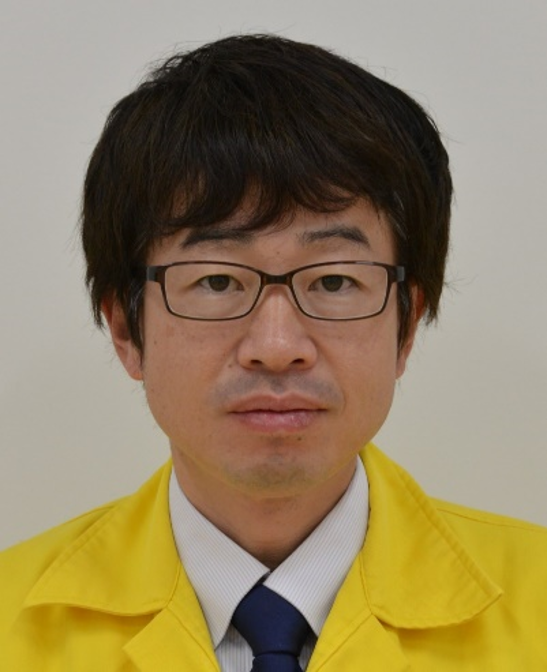
ファナック株式会社 流石 義人氏
2017年FANUCに入社し、FIELD systemの拡販に従事し、日本における製造業のDX推進状況の実態を知る。2022年7月 FIELD system開発次長に就任し、営業経験を活かし、現場改善に必要なデータ収集への壁を排除したデータ基盤であるFIELD system Basic Packageの開発を指揮。
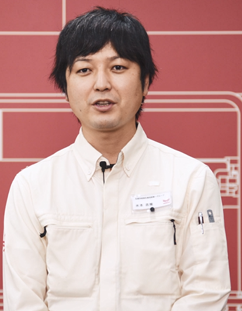
ヤンマーパワーテクノロジー株式会社 水本 吉隆氏
2009年にヤンマー㈱に入社し、ガスタービン機関製造工程の生産技術担当者として工程設計や新機種開発に従事。 生産技術者としての知見を活かしながら現在は工場DXの推進担当者として、工場メンバーと共に尼崎工場のスマート化に向けた活動をリーダーとして推進中。
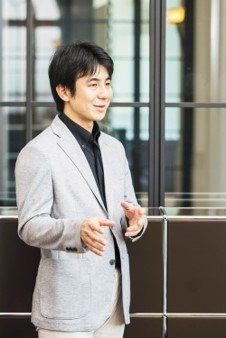
株式会社NTTデータ 法人コンサルティング&マーケティング事業部 シニアスペシャリスト 政井 佑介
製造業で設計・生産技術・生産管理・経営企画・IT戦略などを実務担当として幅広い業務を経験後、2021年にNTTデータに入社し、製造業向けのコンサルティングに従事。 事業会社での知見を活かしながら現在は製造現場の改善支援など、デジタルツールの有効活用に繋がる改善活動の支援や現場向けのデジタルツール企画・開発支援を中心にコンサルティング活動を実施中。
製造現場が抱える一般的な課題
課題・解決策の方向性
政井「製造業では改善活動やTPM活動など、もともとデータを活用する文化は根付いているように思われます。今後は必要に応じてデータを取る方法からIoTなどを通じて常時モニタリングで異常を発見し、改善の効果も取っていく方法が有効となります。そうするためには、ITとOTの連携は非常に重要になってまいります。
例えばITシステムの作業着完データや品質記録データとOTシステムの設備稼働データを組み合わせることで、変化点管理に必要なデータを自動的に蓄積し、問題が起こった時には過去の振り返りも同じデータを用いて行うことで改善を加速することが可能になってきます」。
対談形式による事例紹介
政井「ここからは2人のゲストの方から具体的な事例をご紹介いただきます。ヤンマーパワーテクノロジー株式会社の水本さん、そしてファナック株式会社の流石さんです。まず水本さんよろしくお願いします」。
ヤンマーパワーテクノロジー様 事例紹介
水本「ヤンマーグループは多くの製品群を製造しておりまして、私はエンジン事業に属しています。こちらがヤンマーの組織図ですが、この中にヤンマーパワーテクノロジーがあり、会社は尼崎にあり尼崎工場が中心となっています。製品としてはディーゼルエンジンでは最大63トン、また回転数3万回転のガスタービンなど、規格公差や精度に厳しい部品を作っております」。
水本「下の図はガスタービン機関向けの機械加工部品を作っている図です。約40の品種を25台の設備でジョブショップ生産をしており、1つの設備で複数の工程や複数の品種に対応していました。また加工品としては難削材、薄物、高精度など加工が難しく属人化しがちになるという特徴がありました。加えて、職制の進捗管理業務はさまざまなところから情報を仕入れ、それを自分で台帳を作って管理していたため、現場まかせの判断や管理になって負担をかけていました。同時に生産性の改善の要望もありましたので、これらがDX推進のきっかけとなりました」。
水本「そして現状として、進捗把握のリアルタイム化はできあがっており、データによる業務支援などで工場DXが現場に馴染むところまで来ています。
具体的には全工程の着手・完了のタイムスタンプを収集し、仕向け先のデータを紐づけています。素材が入ってきてから後工程に引き渡すまでの工程の着手・完了の信号をすべて揃えています。生産進捗状況の把握の面では、1つのエンジンを組むために複数の部品が必要ですが、それらが全て揃わないと次の工程に引き渡せないので、各品種の進捗を同期させています。今はタイムスタンプを使ってアンドンや在庫量変遷を可視化することで、出荷量と素材の供給量の同期が図れないかを探っているところです。
また着手・完了のデータを取ることによって、どの設備・工程でどの製品の加工が行われていたか、その間の振動や電流といったセンシングデータや、工具の使用状況を作業実績や品質検査結果と紐づけして稼働や品質改善に向けた分析をしていこうとしているところです」。
政井「DXが現場に馴染んでいるということですが、工場DX推進のきっかけや工夫された点をお教えいただけますか?」
水本「自分が実際にIoTツールを使うことで仕事がやりやすくなったというのが、きっかけの1つです。機械加工で使う切削工具がありまして、どれだけ条件や手順を揃えても要因をすべて管理することが難しく、切削工具が折れてしまうなどのトラブルが発生しました。それで現場に呼ばれて行くんですが、そこには折れた工具しか残ってなくて、原因が分からないわけです。原因を探るにはやはりその瞬間のデータを取っておく必要がある、ということでファナックさんのFIELD systemなどIoT製品を活用してデータを収集して対策までつなげることができました。そこで要因調査のアプローチが変化したというのが1つのきっかけです。
具体的にどう変化していったのかですが、課題把握のために既存データでの見える化と現場メンバーのヒアリングを実施していきました。そのなかで将来のあるべき姿に対して何の業務でどんな課題を持っているかをみんなで共有していきました。そして既存のデータを見える化することによって、ある程度の課題に対する気づきが得られることを確認していただきました。最後に職制の管理業務を中心に職務プロセスを可視化していきました。同じ地図を見ながらディスカッションできることで話がすごく弾むということで、現場とのコミュニケーションツールとして非常に役立ったと思っています」。
政井「今後はどのように工場DXの活動を推進していくのかお聞かせ願えますか」。
水本「進めていくにあたっては納得感というものが重要です。関係者が理解し、納得していただくことに力を入れています。そして今後は工程とラインと工場を分けてレイヤーを整理して、データ処理にはAIの活用なども含めながらデジタルツインの実現に向けて進めていきたいと考えております。現状ではラインの着手・完了データは取り始めていたり、FIELD systemなどで設備1台1台のデータも取り始めていたりしますので、このあたりをどんどん突きつめて進めていきたいと思っています」。
ファナック様 事例紹介
政井「続きましてファナック様の事例紹介に移っていきたいと思います。ファナック様というとFIELD system Basic Packageという製品を販売されていますが、自社の工場・現場でも自分たちの製品を使って改善を進めていらっしゃると伺っています。そうした活動内容や成果事例をご紹介いただけますでしょうか」。
流石「まず当社の紹介をさせいただきますと、ファナックは富士山のふもとに本社を構えており、創立は1972年です。製品としては、工作機械の頭脳であるCNCをはじめ、ロボット、工作機械のロボマシンがあります」。
流石「さきほどご紹介のあったFIELD system Basic Packageという製品も開発しております。さきほど共通言語化というお話がありましたが、この製品はデータを整理して取り、みんなが同じデータを共通言語として活用できるようにするというものです。加工工程だけでなく成型、組立といった工場にあるさまざまな設備をつなげ、データを見える化して外部で使えるようにしています」。
流石「ここからはFIELD system Basic Packageを使ったファナック工場での改善活動をご紹介させていただきます。工場では全員が『現場の、現場による、現場のためのカイゼン活動』というスローガンのもと活動しています。ツールから入るのではなく、現場の課題に生産技術が寄り添って、見える化を行い、必要に応じて短時間で自分たちで管理画面を開発するということを行っています。
工場にはさまざまな設備がありますが、そのデータをFIELD system Basic Packageで収集し、ExcelやBIツールなどの外部ツールを使って収集したデータ を活用しています。ファナック工場では現在、27建屋で約100を超える事例がありますが、標準ツールや共通言語があることによって成功事例をこれだけ横展開できているわけで、FIELD system Basic Packageはそういった役目を担っています」。
流石「では具体的な事例をご紹介します。最初の事例はサーボアンプ工場の事例で、複数台のロボットが連携してサーボを組み立てる工程になります。課題としては、ロボットならびにPLCを含めた稼働状態の把握が困難で、加えて工場が広いため工程をまたいだ可視化が必要でした。しかし複数台のロボットに加え、周辺機器の状態をチェックして1つのステータスを表現するような汎用的なアプリケーションは世の中になかったため、自分たちでそういった仕組みを作りました。それが下の画面です。工程をまたいだ工場全体の稼働監視画面になっています。それぞれのセル単位の状態、さらに深堀りしてオペレータの管理単位で表示することができます」。
流石「下の画面は実際に組立設備で使っている画面ですが、現場の担当が遠くから見た時でも進捗率がどのくらいか一瞬で分かるようにしたいという要望がありました。そこでフラスコの形にして、満杯になったら100%でその日の生産が終わったということが見えるようにしています。また設備がアラームを起こした際には現場にいる担当者のPHSに連絡する仕組みもありまして、ITシステムとやり取りして繋ぐといったこともやっており、ITとOTとの融合を実現した事例になっております。
この他にも毎月の稼働率報告では生産稼働率やロボットのアラームの集計やアンプの試験の不良率を自動集計できるようにしており、選択するだけで報告書が完成できるようになっています」。
流石「次は場所を変えて隼人工場の事例をご紹介します。こちらの工場ではパルスコーダと呼ばれるものを生産しているのですが、組立工場2棟と加工工場1棟という複数建屋に工程がまたがっています。そのため稼働状況の把握に移動が伴い、しかも約50台の設備を20名弱のオペレータで管理・運用しなくてはなりませんでした。
そこで広範囲の設備の稼働状況を見るために作ったのが下のモニタリング画面です。生産数のグラフ表示では、現場の方はパトライトの状態に意味を持たせているので、パトライトの信号の色をそのまま表示してほしいという要望に応えたものです。目標生産計画に対して今どのくらいの生産数まで行っているかが一目で分かるようになっています。
またNG品が品質で出た時にロボットが払い出してNG品の箱に入れるのですが、箱がいっぱいになりそうになったらオペレータに直接連絡することで生産を止めないようにする、という活動もしています。このあたりもITと連携して、設備側から自発的にオペレータに気づきを与える取り組みとなります」。
流石「この他に、機械加工工場での活用事例をご紹介します。クーラントの希釈装置が別室にあるため運転状態を外部から把握するのが困難でしたが、FIELD systemでデータ収集し、ドラムの残量が設定したしきい値を越えたらユーザーに通知する、という仕組みです。それまでは1日に2回現地に行って残量を確認して、不足していた場合にはクーラントを足すという行動をしていたのですが、これによって設備側で気づきを飛ばしてくれるといった形になっています」。
流石「この他にも、例えば加工工場の空気環境の改善では、それまでポータル粉塵計を持って人が歩いて測定していたのを、測定コストがかかるしリアルタイムではないということで環境センサを設置して自動測定していたのですが、内部メモリに保存したデータを定期的に回収する手間がかかるということで、環境センサのデータをNode-Redで収集して見える化する仕組みも自分たちで作り上げました。データとデータが紐づくことによって、稼働率が高い時は空気の環境が悪くなるという新たな気づきを得て、ではあそこを改善しようということになりました。標準データと外部のデータの共通言語化は非常に重要だと思っています。
さらに、この他にもプリント基板を吸着して搬送する際に、これまではロボットが基板を落とすまでは交換時期が不明だったのですが、ロボットに真空圧計を取り付けてデータの異常値を見て落とす前に交換することができるようになりました。本日は皆さまに共通しそうな事例をご紹介しました」。
政井「ありがとうございました。こういった事例に取り組む上で、関係者の協力をどう得るかといった点がすごく難しい点だと思うのですが、そのあたりで重要だったことは何でしょうか」。
流石「IoTによる改善活動には、やはり推進役が必要かと思います。先ほどのヤンマーさんであれば、水本さんがそれに当たると思います。これまでITを使っていなかった製造部門にIoTを使っていただくためには、現場の課題にまず寄り添うというスタンスと、現場の『こういうことをやりたいんだ』に対して、『ではこれでどうですか』と迅速に提案できるスピード感で、興味を持ってもらってとにかく1度使っていただくことでハードルを下げていくことが必要だと思います。
そこで社内ウェブサイトで事例の公開など必要な情報の共有をしている他、ファナックではFIELD system Basic Packageを標準ツールとして使っておりますので、稼働監視など利用頻度が高い事例をサンプルアプリとして配布して横展開も非常にやりやすくしています。
また、DX推進ですとかIoTによる業務改善というのは、時に孤独というか、なかなか成果発表する場がないという声も多くお聞きします。そこでまだ始めて間もないのですが、FIELD systemのユーザー様同士の交流会を企画して、皆さまの改善活動を共有していただく取り組みもしております」。
政井「ありがとうございます。流石さんご自身が開発部隊やIoTとOTの橋渡し役をされたことが、うまくいったきっかけの1つだったのかなと思います。お二人のお話をお聞きして共通していると感じたのは、スモールスタートをしながら活動を大きく広げてこられたということ。そして,そのために必要なのは、環境づくり、協力者づくり、そして共通言語として理解可能な情報の準備だったのかなと思います。そのあたりでの工夫について改めてお聞かせください」。
水本「上司や同僚であったり、一緒に取り組んでいく現場のメンバーであったり、人や環境というのは本当に大切だな、と思いました。ファナックさんのご紹介を見ていてすごくいいなと思ったのが、社内外のコミュニティづくりですね。DX推進担当は各拠点にそんなに多くないので、割と孤独にやってらっしゃる方も多いんじゃないでしょうか。私も社内外問わず、同様な仕事をやっておられる方々との関係を大切に作っていきたいと思っています」。
流石「ヤンマーさんの改善活動などを拝見させていただいて、やはりまず誰かがやってみようと言って始めることが必要かなと思います。その時のやり方にもいろいろあって、水本さんからさきほど業務フローを描いたというお話があったんですが、あれはまさにその通りだなと思いました。共通の地図の上で共通言語を使って、オペレータ目線であったり保全班目線であったり、また横展開していくうえでも共通言語や、それを可能にするプラットフォームを活用していくことが重要かなと思います。そうしてみんなで取り組んで、みんなで成功したという納得感がないと、なかなか継続しての改善は難しいと思っております」。
まとめ「NTTデータ×FANUCによる改善サポート」
政井「ありがとうございました。最後にまとめとなりますが、課題解決には、上司の協力や仲間とオープンな対話ができる環境づくり、自分からやりたいと言う人づくり、そしてみんなが理解できるような情報をシェアできる共通言語の3つの要素が必要かと思います。それを実現するには、お客様目線-これは商品のお客様だけでなく、後工程もお客様ととらえることが重要です。そして社内だけでは解決できないことを社外に協力に求めてコミュニティの中で実現していくこと。そのためには社内外のつながりも重要です。そして共感・納得感・腹落ちといったところも重要で、それを全員で行った結果、モチベーションも上がっていき、相互理解とチームワークによって壁が破壊できて、さらに継続的に成果が上がっていくという良いサイクルに入っていくのではないかなと思います」。
政井「最後に少し宣伝となりますが、NTTデータとファナック様が協力して、改善サポートサービスというものを始めます。こちらはFIELD system Basic Packageを核としたサービスで、IoT側、エッジ側はファナック様のご協力をいただき、NTTデータはIT側、製造実行のMESや、PLMとかERPに代表される業務システム側をうまくつないでいく役割を担いながら、可視化やセキュリティのサービスを展開していきたいと考えております」。
流石「核となるFIELD system Basic Packageは、4M*のデータを常時モニタリングで手間をかけずに取得できる、プログラムの終了時や上位の生産指示など変化点と紐づけたデータを蓄積できる、みんなで同じデータと同じ仕組みを仕様して組織的な改善ができるといったところが特徴となっております」。
*4MとはMan(人)、Machine(設備)、Material(原材料)、Method(工程・工法)のこと
政井「このFIELD system Basic Packageをうまく使いながら、工場全体、会社全体のさまざまな改善をサポートしてまいりたいと思っております。NTTデータに足りない知見である工場側OTに関してはファナック様のサポートをいただきながら2人3脚で取り組んでまいります。よろしくお願いします」。
-
お問い合わせはこちら
お問い合わせはこちら -
本セミナーのアーカイブ動画を
動画視聴のお申し込みはこちら
ご視聴いただけます
過去のセミナー
-
LITRON® Sales最新動向・事例紹介 ~セールス領域における生成AIによる飛躍的成果創出のカギ
-
生産領域における業務・情報のサイロ化を解決!製薬業界における品質保証業務の最適化